Legatec
Expertise, Innovation und Qualität: Die Legatec Composite GmbH mit Sitz in Enzesfeld-Lindabrunn baut Composite (Faserverbund)-Teile für die Königsklassen des Automobilsports und die (unbemannte) Luftfahrt – von der Konstruktion über die Entwicklung von Prototypen bis hin zur Produktion von Kleinstserien.
Unsere Beziehung zum Projekt
- Unterstützung bei Digitalisierungsförderung
- Förderstellenkontakt
„Am Anfang steht ein Plan, stehen Ziele. Doch um diese zu verwirklichen, braucht es viel Einsatz und Leidenschaft“, sagt Carsten Gäbler, Geschäftsführer der Legatec Composite GmbH in Enzesfeld-Lindabrunn (Bezirk Baden). „Das gilt für die Selbstständigkeit genauso wie für die Entwicklung und den Bau unserer Composite-Teile.“ Der Unternehmer sitzt auf einem gemütlichen Sessel im offen gestalteten Besprechungsraum seines Betriebes und erzählt von den Anfängen des Unternehmens, von Mut und Visionen und davon, wie viele Rädchen ineinandergreifen müssen, bis aus der Idee der Kunden verbaubare Teile entstehen.
Kontakt
Legatec Composite GmbH
Birkengasse 6
2551 Enzesfeld-Lindabrunn
+43 2256 81 800-10
Jetzt kontaktieren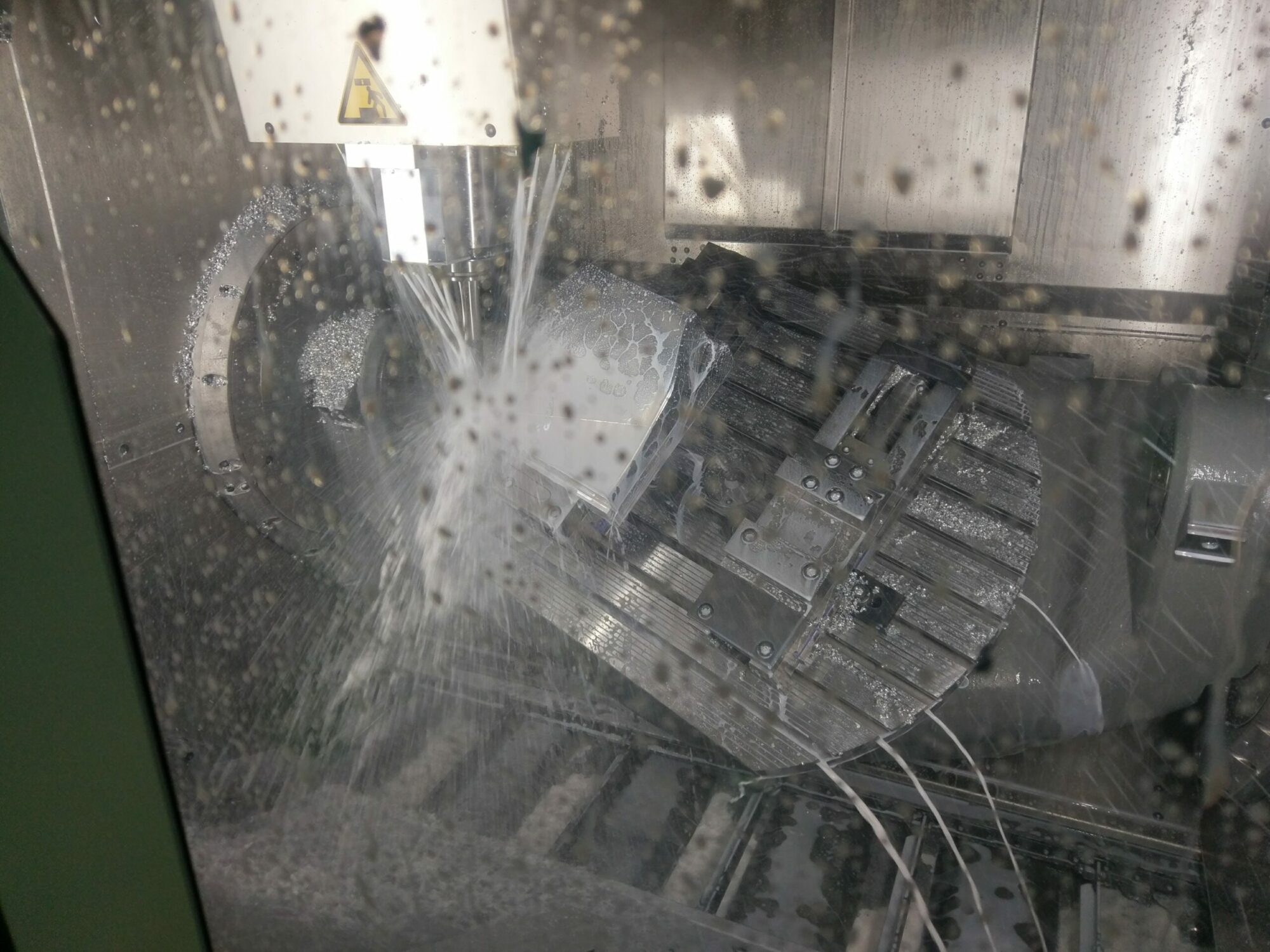
Eine breite Produktpalette im Bereich des Leichtbaus
„Die Idee zur Selbstständigkeit begleitet mich schon mein halbes Leben. Doch erst 2013, mit Mitte 40, habe ich diesen Schritt gewagt“, blickt Gäbler zurück. Mit langjähriger Erfahrung im Bereich des Leichtbaus sowie zahlreichen Kontakten in der Branche war die Ausrichtung des Betriebs klar. Hauptmärkte von Legatec sind vor allem der Automobil-Rennsport und die Luftfahrt, hier hauptsächlich auch der boomende Bereich der unbemannten Luftfahrt. „Vom Anlagen- bis hin zum Bau von Strukturbauteilen für den Schwermaschinenbau decken wir quasi den ganzen Bereich ab, der mit Leichtbau zu tun hat. Leichtbau von Einzelkomponenten kann hier drei Gramm, aber auch 300 Kilogramm bedeuten“, erklärt Gäbler und versucht zu verdeutlichen: „Nehmen wir beispielsweise einen Formel-1-Boliden her. Die heutigen Fahrzeuge in der Königsklasse bestehen zum Großteil aus Composite-Material, bei modernen Passagierflugzeugen sind es bis zu 40 Prozent – die Flügel von Windkraftanlagen etwa bestehen zu einem noch größeren Anteil aus diesem Material.“
Composite, oder zu Deutsch Faserverbund, ist eine Komposition aus mehreren Materialien mit ganz unterschiedlichen Eigenschaften. „Die vielfältigen Möglichkeiten, die sogenannten ,Reinforcements‘ (Verstärkungsmaterialien) mit verschiedenen Matrixsystemen (Einbettmassen) zu kombinieren, sorgen für die ganz besonderen Eigenschaften der daraus entstehenden Bauteile“, erklärt Gäbler und führt in den rund 1.000 Quadratmeter umfassenden Entwicklungs-, Konstruktions- und Produktionsbereich.
„Vor sieben Jahren, als wir zu zweit gestartet sind, hatten wir beispielsweise nur einen Konstruktionsarbeitsplatz, keine eigene Bauteilberechnung, keine Qualitätsabteilung mit Maschinen, um die Bauteile zu vermessen.“ Heute deckt das Unternehmen mit 16 Mitarbeitern am Standort in Enzesfeld-Lindabrunn von der technischen Entwicklung, über die Bauteilauslegung, oder Optimierung, dem eigenen Werkzeug-und Vorrichtungsbau, über die daraus entstehenden Prototypen bis hin zur Kleinstserie den gesamten Prozess im eigenen Haus ab.
Tüfteln im Bereich von High-End-Elektroantrieben
Die Bandbreite an Entwicklungen und Produkten ist groß: Monocoque, oder Rotorblätter für Drohnen gehören ebenso zum Portfolio wie Entwicklungen auf neuen und innovativen Sektoren, oder der Elektrifizierung des Rennsports (Formula E). „Vor allem im Bereich von High-End-Elektroantrieben sind wir gerade am Tüfteln“, verrät Gäbler mit lauter Stimme, um den Lärm der Fräsen und Zerspan-Maschinen in der großen Fertigungshalle zu übertönen.
Während ein paar Räume weiter Mitarbeiter im „Gehirn des Unternehmens“, wie die Konstruktionsabteilung genannt wird, konzentriert vor ihren Bildschirmen sitzen, überwachen Sensoren im Assembly-Bereich penibel Temperatur und Luftfeuchtigkeit. „Hier werden die einzelnen Komponenten und Teile zu einem komplexen Ganzen zusammengebaut“, erklärt Gäbler – ähnlich einem Bausatzkasten. „Nur mit dem Unterschied, dass wir das in einem viel größeren Maßstab machen und auch die Einzelteile selbst entwickeln und fertigen.“ Denn bis aus einer Vision ein fertiges Bauteil entsteht, das beispielsweise auf den Rennstrecken dieser Welt zum Einsatz kommt, ist es oft ein langer Weg.
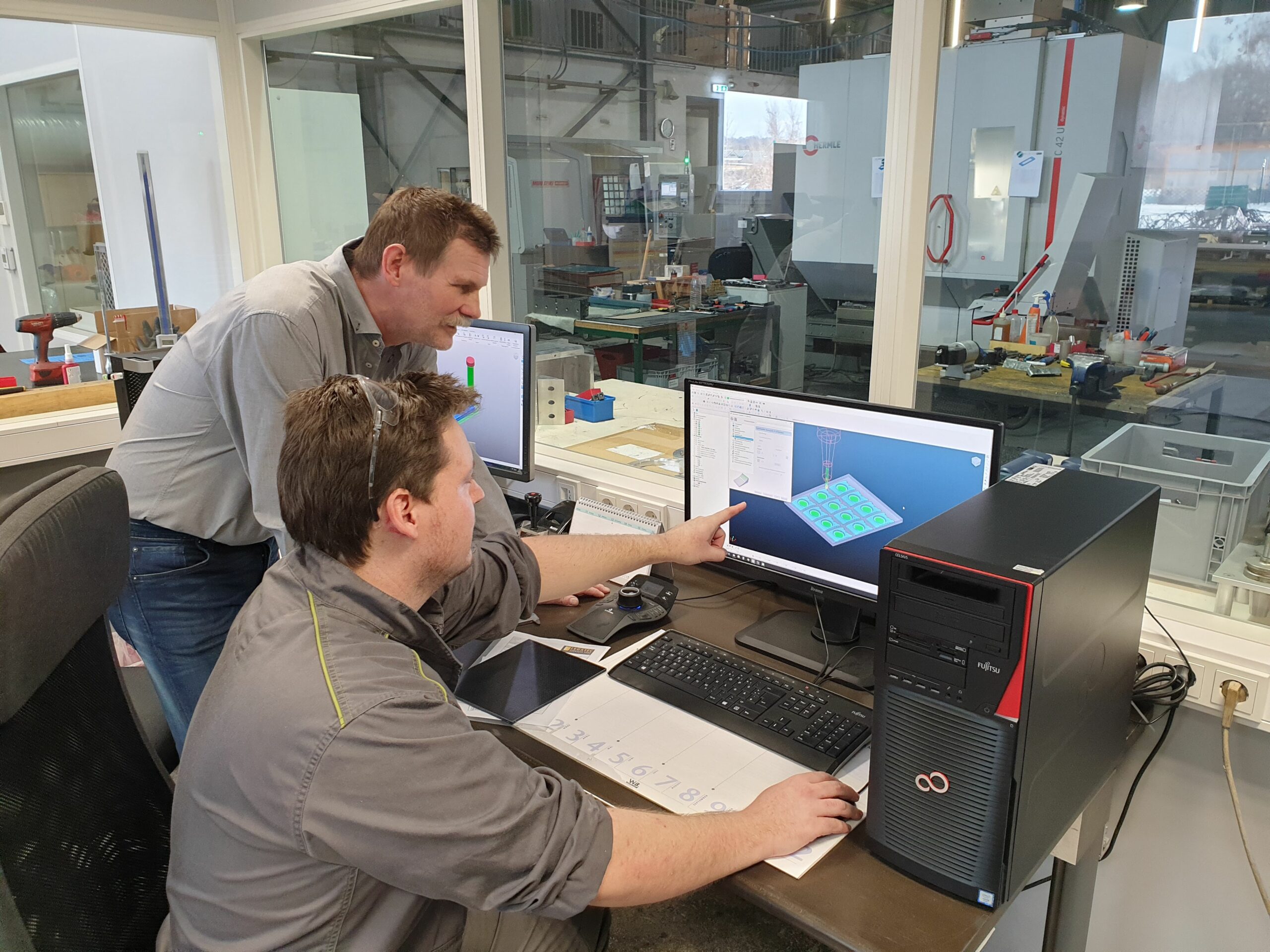
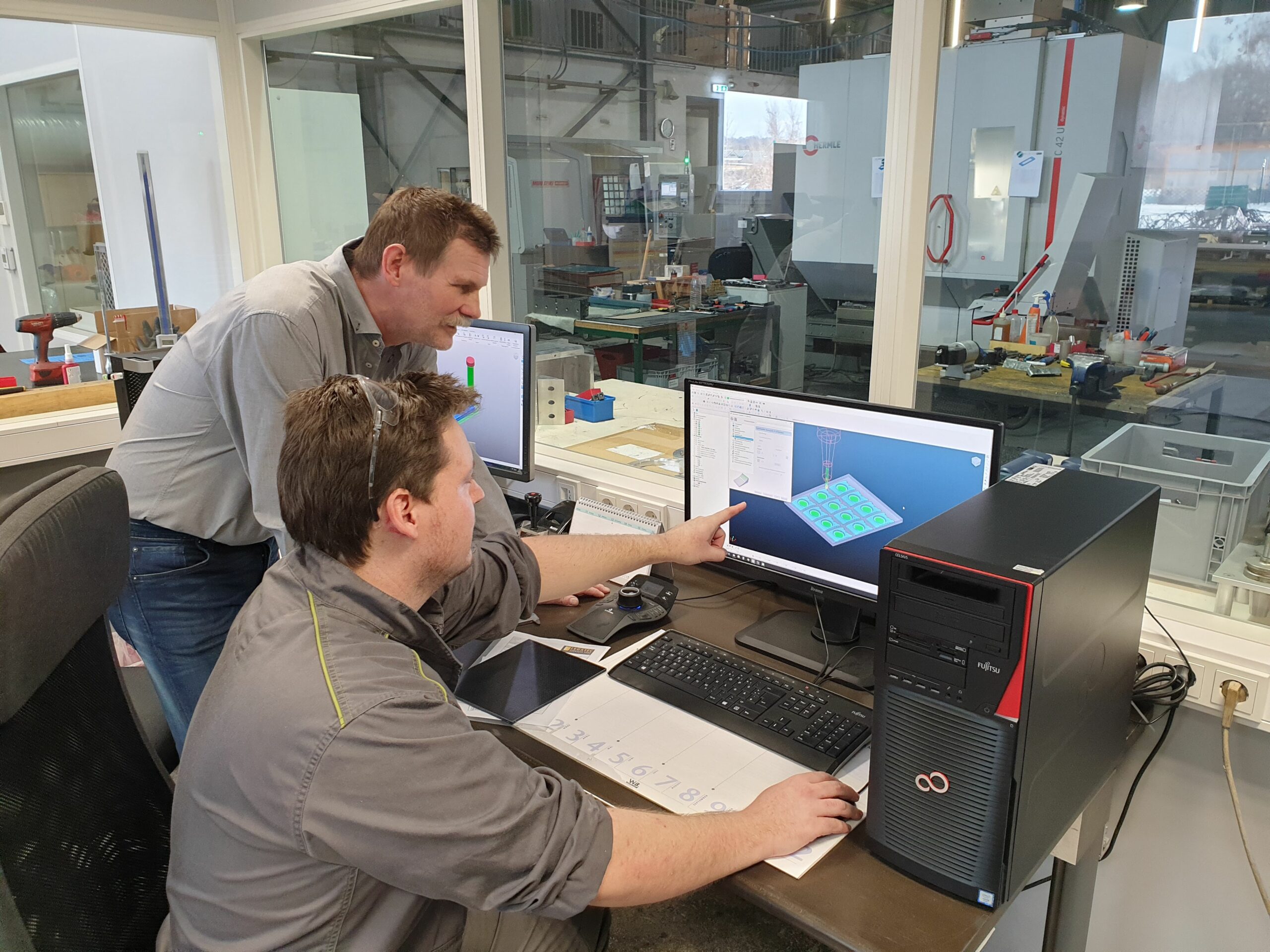
Tüfteln im Bereich von High-End-Elektroantrieben
Die Bandbreite an Entwicklungen und Produkten ist groß: Monocoque, oder Rotorblätter für Drohnen gehören ebenso zum Portfolio wie Entwicklungen auf neuen und innovativen Sektoren, oder der Elektrifizierung des Rennsports (Formula E). „Vor allem im Bereich von High-End-Elektroantrieben sind wir gerade am Tüfteln“, verrät Gäbler mit lauter Stimme, um den Lärm der Fräsen und Zerspan-Maschinen in der großen Fertigungshalle zu übertönen.
Während ein paar Räume weiter Mitarbeiter im „Gehirn des Unternehmens“, wie die Konstruktionsabteilung genannt wird, konzentriert vor ihren Bildschirmen sitzen, überwachen Sensoren im Assembly-Bereich penibel Temperatur und Luftfeuchtigkeit. „Hier werden die einzelnen Komponenten und Teile zu einem komplexen Ganzen zusammengebaut“, erklärt Gäbler – ähnlich einem Bausatzkasten. „Nur mit dem Unterschied, dass wir das in einem viel größeren Maßstab machen und auch die Einzelteile selbst entwickeln und fertigen.“ Denn bis aus einer Vision ein fertiges Bauteil entsteht, das beispielsweise auf den Rennstrecken dieser Welt zum Einsatz kommt, ist es oft ein langer Weg.
„Am Anfang steht ein Plan, stehen Ziele. Doch um diese zu verwirklichen, braucht es viel Einsatz und Leidenschaft.“
Fotocredit: Legatec